Industry
The Power of Automation: How Welding Machines Are Changing Manufacturing Processes
Apart from gas welding, all major welding processes use a welding machine to create an electrical arc and the required temperatures to fuse two metals together. If you’re just getting started, choosing the right equipment, including the welder that best suits your needs, maybe the hardest part. Just as there are several welding processes, there are also several types of machines, with each suited to different metals and the environments where they’re used. So, a bit of background knowledge can save you quite a bit of cash and get the expected results in any task you undertake.
Welder Types
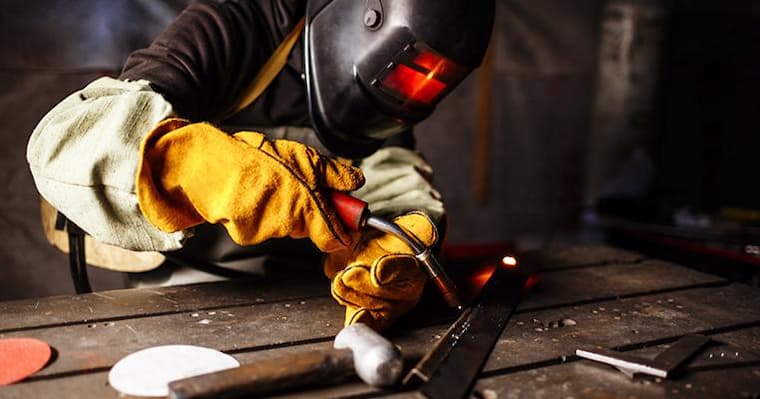
Anyone on the lookout for welding machines Australia is spoilt for choice. The major categories in this respect are stick, TIG and MIG machines. Multi-purpose variants additionally let you do several types of jobs with a single machine, so help with versatility. Let’s dig deeper.
Stick Welders
Stick or arc welders are used in many construction and repair jobs, especially where cast iron and thicker ferrous metals are involved. The machine generates an electric current in the gap between the electrode and the workpiece. This can be altered in polarity between DC, AC or AC/DC so can produce both fast results and strong welds with deep penetration. One major benefit is that there’s no need for shielding gases, meaning stick welders are good for both indoor and outdoor use, especially in open areas with a lot of wind. Another is that it gets good results in less-than-perfect metals affected by rust or surface damage.
It’s not all roses though. Stick welders can produce a lot of spatter, so more work in cleanup, and are more in tune with thicker workpieces, usually 1.5mm or more. The process also involves a steeper learning curve, particularly the skill to maintain a stable arc. On the whole, though, stick welding is a general-purpose process good for most applications, and stick welders are some of the more compact and affordable options there are.
MIG Machines
MIG welders, and the process in general, are easier to master. The machine automatically feeds wire through the gun and helps create the arc. This wire then fuses with the base metal to create a strong, cleaner weld, generally free of spatter. The process is versatile, so it can be used on steel, stainless steel and aluminium and in much thinner pieces compared to stick welders.
The same machine can additionally be used with flux-cored wire where there’s the need to shield the base metal from external contaminants without the use of shielding gases. This method is simpler and can be used in areas and conditions where gas cylinders pose a risk or are harder to transport. On the whole, MIG welders should be the go-to choice for welders looking for cleaner, stronger welds that don’t take much time to get right, and in thinner metals.
TIG Welding Machines
TIG welders offer the best control, both of the arc with consistent current levels and weld strength. The process uses a non-consumable electrode that holds the arc and gets very high temperatures to get exceptionally clean welds in very thin sections of alloyed steels, stainless steel, and non-ferrous metals with higher melting points, such as magnesium, copper and titanium. Compared to other welders, this machine allows for the highest quality welds. superior strength and results that require no cleaning.
If you’re still having difficulty deciding which metals you’ll be working with, metal thickness and where most of the work is done, a good option for beginners is a multi-purpose or combo welder. This is a versatile, general-purpose welder good for various jobs involving different metal sections. MIG and stick, and TIG and stick are the most common, but buyers of welding machines Australia can also find MIG and TIG combos at somewhat higher prices.
What to Look for in Your Next Welder
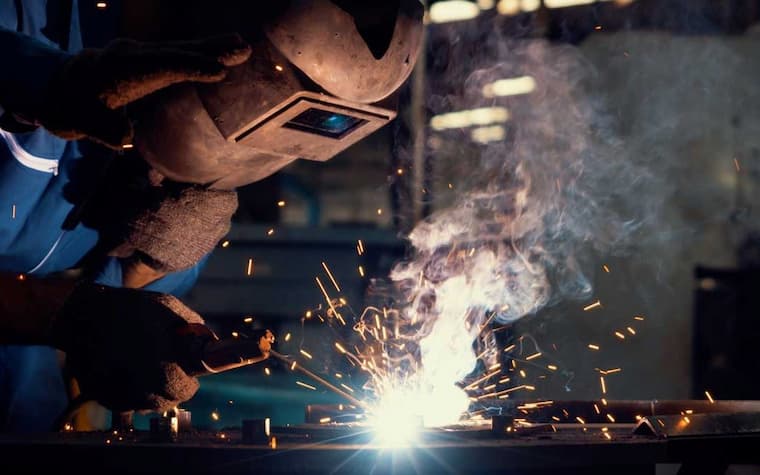
The huge price differences among different welding machines mean not all are created equal. Amperage ratings, duty cycles and distinct operational, safety and convenience features all determine how much you’ll be paying, but more importantly, the metals you can work with and the strength of the welds. They also impact speed and ease of use.
Amperage refers to the power the machine has on tap, specifically to control the electric arc and how this penetrates the base metal. Machines with more amperage will get faster and neater welds in metals that need more attention in terms of temperatures, as well as thickness. A decent machine will have at least 100 Amps to weld metals about an inch thick. Of course, more is always better, but you’ll be paying for it. MIG and TIG welders generally run on more power, averaging around 200A, so are a bit dearer than general-purpose stick machines.
Duty cycles refer to the length a welder is operational before it needs to cool off. Welding sessions are calculated as a percentage of 10 minutes of non-stop work and the welder running at full amperage. For example, 200A machines with a 50 per cent cycle can safely run on all its 200 amps for five minutes, before risking overheating. Of course, you can dial down the amperage and work for longer. On the whole, duty cycles determine speed, particularly when working on more exotic metals that also happen to be bulkier.
Lastly, consider the extras you’re getting with the machine. Welders with inverter tech offer easier switching between AC and DC, longer duty cycles, more efficiency, smaller footprints and faster welding speeds. In addition, safety features like overload protection and IP21S ratings mean besides the basic welding PPE gear, you’re protected from current surges and outside factors. And convenience additions, such as wire foot controls in MIG welders keep both hands where they should be. Different features enhance usability, so decide what you need and what you can do without. For beginners, packaged deals with machines and all the necessary gear like torches, hoses, regulators, valves and clamps, will get you working sooner rather than later. While seasoned pros can select parts and accessories that best suit their needs.
